Posted: Oct 06, 2015 5:27 pm
Some Basics
Wood is the principle material used for building steel string guitars. There are many good books that will teach you all you would ever want to know about wood. For the serious enthusiast I would recommend:
Understanding Wood: A Craftsman's Guide to Wood Technology by Bruce Hoadley.
For steel string guitars typical construction uses a soft wood (spruce or cedar) for the top and a hardwood (rosewood, mahogany, koa, maple etc.) for the sides and back. Mahogany or Spanish cedar are used for the neck. To be sure, other woods can also be used.
Here are some popular choices for top wood. Red spruce also known as Adirondack spruce was used by Martin in their “golden era”. Eventually red spruce was no longer available and it was replaced by Sitka spruce. Today many steel string acoustic guitars are built with Sitka spruce tops but red spruce is once again available in limited supplies.
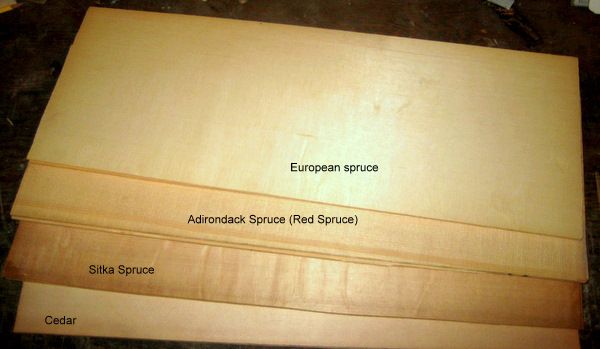
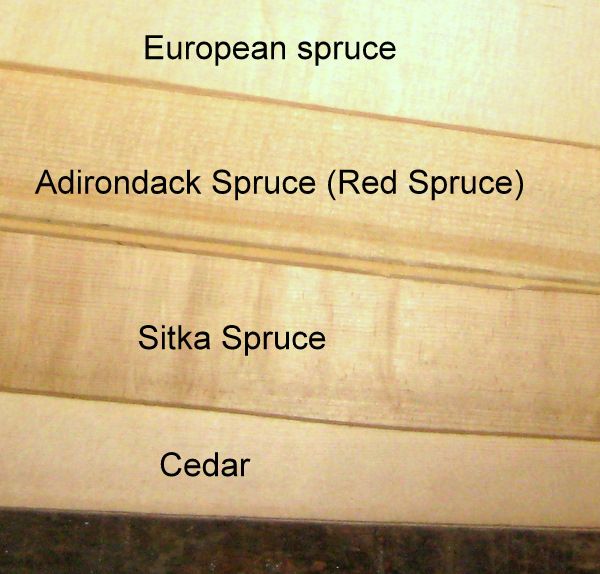
For someone building their first guitar I would strongly recommend, Sitka spruce for the top wood. Indian rosewood for the sides and back. Honduras mahogany for the neck. There are many reasons why I like those choices, suffice it to say that I think they give you the best chance of ending up with a guitar that you'll be happy with. Of course, if you just don't like the sound of a rosewood guitar then perhaps that wouldn't be a good choice for you.
Tone Wood
In the guitar world you'll often, and I mean often, come across the phrase “tone wood”. It's meant to refer to magical wood with magical qualities destined for instruments. Let me see, how should I put this- there's no such thing as “tone wood”. To be sure, some wood is a better choice to use for guitars than other pieces of wood, and different types of wood tends to make different sounding guitars. But you can find good wood for building guitars from someone who isn't selling “tone wood.”
The best way to get a sense of how different types of wood sound when they're used for guitar construction is to play different guitars made with different kinds of wood. Most people quickly get the idea.
What makes wood suitable for a guitar.
Stability
For reasons which should be pretty obvious you want the wood used to be as stable as possible. That is, you don't want it shrinking and cracking. You don't want the neck warping this way and that. You want it to stay the way it was built.
The way you cut a piece of wood out of the tree it grew from can go a long way in resulting in a very stable piece of lumber. To make a long story short, quartersawn lumber is the most stable. The picture below shows how quartersawn lumber is harvested radially from a log. The result is long straight vertical grain lines running the length of the board. These grain lines are perpendicular to the the edge of the board.
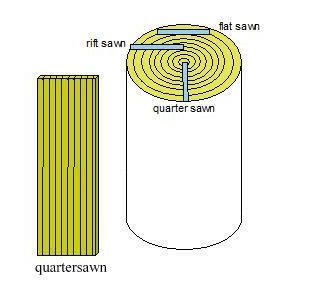
The more perpendicular the grain lines the more strength the board will have across the grain. Good guitar wood is “well quartered” wood for the top, back, sides, and neck.
Moisture content
I won't go into all the details here unless there's a request to do so, (google or read Hoadley's book for the rest of the story) but wood will take on or give off moisture depending on the relative humidity (RH) of the environment it is in. As wood takes on or gives off moisture it stretches or shrinks. Because the parts of a guitar are glued in place they have a limited tolerance for this stretching and shrinking before cracking comes into the picture. Some construction techniques can help this a bit.
The guitar builder and player must be aware of this hygroscopic property of wood. For the builder it means, wood ,must be dry enough before it is used to build an instrument. The instrument must be built in an environment where the RH is controlled. A range of 40 to 55 RH would work. Some very good builders go a lot lower. It's not a good idea to build in higher RH. The moisture content of your wood should be around 6-7 percent before you use it. Wood sitting in an RH of 40-55% will eventually get there.
Aging also effects wood as resins harden. This is know as seasoning. I won't say much about this other than “season to taste.”
I would recommend that a new builder buy wood from a luthier supplier and then keep the wood in an RH controlled environment throughout the build unless you know enough about wood to go it on your own.
I'll talk more about specific kinds of wood as I build.
Tools
You'll need some tools to build a guitar but you won't need as many as you'll see me use as I build. I have no good explanation as to why that is so. Also, although nice tools are nice, you don't need fancy tools to make a guitar. It is far more important to have a well sharpened blade or a well setup plane than a particular brand of tool. I think this tutorial would be better if I didn't use some of the more exotic and expensive hand tools – at least I don't use any fancy power tools. At some point I'll put together a basic list of tools needed but it really all depends on individual preference. Some tools work well for some folks and not others- such is life. Like every other aspect of guitar building it takes trial and error and experience to know what works for you. I'll talk more about specific tools as I go along.
Glue
With the possible exception of the neck joint the guitar is held together with glue. Traditionally hot hide glue was used. Hot hide glue has been used for centuries and it works. There's a bit of a learning curve involved with hot hide glue but it's not that hard to use. A good alternative glue is Original Titebond. Titebond is readily available, easy to use, and it works. There's nothing wrong with building a guitar using Titebond for the glue.
I'll be using both hot hide glue and Titebond because for me they each have an advantage for certain aspects of the guitar. You can however, substitute one for the other at any place in the build process.
I'll also use a dab of superglue (Cyanoacrylate) from time to time.
Jigs
Unfortunately I use a fare number of jigs in the building process. These can be simple things like side molds which help keep the bent sides aligned until they are glued in place to more complicated things like binding router jigs. It is possible to build a good guitar without any jigs and I kind of feel that this would be a better tutorial if I didn't use any. On the other hand, steel sting guitars as we know them were a factory invention and tooling was and is most definitely used to build them. Even the Spanish classical guitar makers use some tooling to help with construction. In fact, I use some of the Spanish tooling too!
In the end every builder needs to decide for themselves how many jigs, fixtures, tooling, CNC machines is right for them. Ask yourself, why am I doing this and do I really want a factory in my basement.
As I go along I'll mention what tooling I recommend using and what alternative method might substitute.
Perfection
The whole purpose of jigs and tooling is to help make the guitar more perfect. Sometimes lack of perfection will have really bad effects on the usability of the instrument. If the frets are in the wrong place the instrument won't play in tune. If the action is way too high the instrument will be too hard to play. If glue joints are not made well enough they will fall apart. A very good guitar can be made by hand building without the use of specialized jigs. But jigs ,make it easier to do. In the end you need to decide on the degree of perfection you're going for and the building style that you want to engage in.
Enough for the basics. I'll get started building in the next post and I expect there will be more pictures and less words.
Wood is the principle material used for building steel string guitars. There are many good books that will teach you all you would ever want to know about wood. For the serious enthusiast I would recommend:
Understanding Wood: A Craftsman's Guide to Wood Technology by Bruce Hoadley.
For steel string guitars typical construction uses a soft wood (spruce or cedar) for the top and a hardwood (rosewood, mahogany, koa, maple etc.) for the sides and back. Mahogany or Spanish cedar are used for the neck. To be sure, other woods can also be used.
Here are some popular choices for top wood. Red spruce also known as Adirondack spruce was used by Martin in their “golden era”. Eventually red spruce was no longer available and it was replaced by Sitka spruce. Today many steel string acoustic guitars are built with Sitka spruce tops but red spruce is once again available in limited supplies.
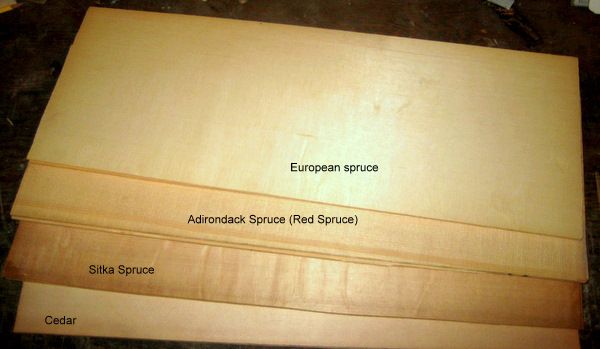
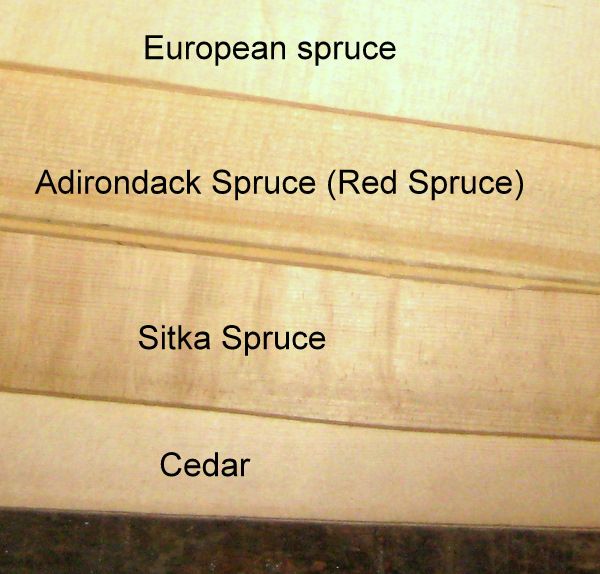
For someone building their first guitar I would strongly recommend, Sitka spruce for the top wood. Indian rosewood for the sides and back. Honduras mahogany for the neck. There are many reasons why I like those choices, suffice it to say that I think they give you the best chance of ending up with a guitar that you'll be happy with. Of course, if you just don't like the sound of a rosewood guitar then perhaps that wouldn't be a good choice for you.
Tone Wood
In the guitar world you'll often, and I mean often, come across the phrase “tone wood”. It's meant to refer to magical wood with magical qualities destined for instruments. Let me see, how should I put this- there's no such thing as “tone wood”. To be sure, some wood is a better choice to use for guitars than other pieces of wood, and different types of wood tends to make different sounding guitars. But you can find good wood for building guitars from someone who isn't selling “tone wood.”
The best way to get a sense of how different types of wood sound when they're used for guitar construction is to play different guitars made with different kinds of wood. Most people quickly get the idea.
What makes wood suitable for a guitar.
Stability
For reasons which should be pretty obvious you want the wood used to be as stable as possible. That is, you don't want it shrinking and cracking. You don't want the neck warping this way and that. You want it to stay the way it was built.
The way you cut a piece of wood out of the tree it grew from can go a long way in resulting in a very stable piece of lumber. To make a long story short, quartersawn lumber is the most stable. The picture below shows how quartersawn lumber is harvested radially from a log. The result is long straight vertical grain lines running the length of the board. These grain lines are perpendicular to the the edge of the board.
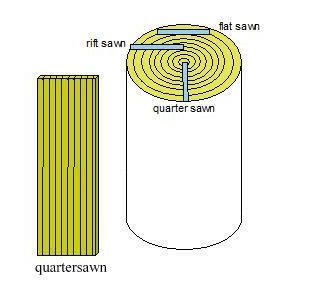
The more perpendicular the grain lines the more strength the board will have across the grain. Good guitar wood is “well quartered” wood for the top, back, sides, and neck.
Moisture content
I won't go into all the details here unless there's a request to do so, (google or read Hoadley's book for the rest of the story) but wood will take on or give off moisture depending on the relative humidity (RH) of the environment it is in. As wood takes on or gives off moisture it stretches or shrinks. Because the parts of a guitar are glued in place they have a limited tolerance for this stretching and shrinking before cracking comes into the picture. Some construction techniques can help this a bit.
The guitar builder and player must be aware of this hygroscopic property of wood. For the builder it means, wood ,must be dry enough before it is used to build an instrument. The instrument must be built in an environment where the RH is controlled. A range of 40 to 55 RH would work. Some very good builders go a lot lower. It's not a good idea to build in higher RH. The moisture content of your wood should be around 6-7 percent before you use it. Wood sitting in an RH of 40-55% will eventually get there.
Aging also effects wood as resins harden. This is know as seasoning. I won't say much about this other than “season to taste.”
I would recommend that a new builder buy wood from a luthier supplier and then keep the wood in an RH controlled environment throughout the build unless you know enough about wood to go it on your own.
I'll talk more about specific kinds of wood as I build.
Tools
You'll need some tools to build a guitar but you won't need as many as you'll see me use as I build. I have no good explanation as to why that is so. Also, although nice tools are nice, you don't need fancy tools to make a guitar. It is far more important to have a well sharpened blade or a well setup plane than a particular brand of tool. I think this tutorial would be better if I didn't use some of the more exotic and expensive hand tools – at least I don't use any fancy power tools. At some point I'll put together a basic list of tools needed but it really all depends on individual preference. Some tools work well for some folks and not others- such is life. Like every other aspect of guitar building it takes trial and error and experience to know what works for you. I'll talk more about specific tools as I go along.
Glue
With the possible exception of the neck joint the guitar is held together with glue. Traditionally hot hide glue was used. Hot hide glue has been used for centuries and it works. There's a bit of a learning curve involved with hot hide glue but it's not that hard to use. A good alternative glue is Original Titebond. Titebond is readily available, easy to use, and it works. There's nothing wrong with building a guitar using Titebond for the glue.
I'll be using both hot hide glue and Titebond because for me they each have an advantage for certain aspects of the guitar. You can however, substitute one for the other at any place in the build process.
I'll also use a dab of superglue (Cyanoacrylate) from time to time.
Jigs
Unfortunately I use a fare number of jigs in the building process. These can be simple things like side molds which help keep the bent sides aligned until they are glued in place to more complicated things like binding router jigs. It is possible to build a good guitar without any jigs and I kind of feel that this would be a better tutorial if I didn't use any. On the other hand, steel sting guitars as we know them were a factory invention and tooling was and is most definitely used to build them. Even the Spanish classical guitar makers use some tooling to help with construction. In fact, I use some of the Spanish tooling too!
In the end every builder needs to decide for themselves how many jigs, fixtures, tooling, CNC machines is right for them. Ask yourself, why am I doing this and do I really want a factory in my basement.
As I go along I'll mention what tooling I recommend using and what alternative method might substitute.
Perfection
The whole purpose of jigs and tooling is to help make the guitar more perfect. Sometimes lack of perfection will have really bad effects on the usability of the instrument. If the frets are in the wrong place the instrument won't play in tune. If the action is way too high the instrument will be too hard to play. If glue joints are not made well enough they will fall apart. A very good guitar can be made by hand building without the use of specialized jigs. But jigs ,make it easier to do. In the end you need to decide on the degree of perfection you're going for and the building style that you want to engage in.
Enough for the basics. I'll get started building in the next post and I expect there will be more pictures and less words.