Time to make some more of the bits that go with the sides. I'll start with the linings. Now that the sides are only about 2mm thick (and we're going to cut that away when we route for the bindings) we need something to keep the top and back attached to the sides- that's the job of the linings.
Common wood for linings are: mahogany, basswood, and Spanish Cedar, which is what Martin uses and what I'll be using. Spanish cedar is light and it smells nice too. Willow is common lining for violins and also a fine choice- but it doesn't smell all that great. Willow is what my teacher liked - I imagine he got that idea from his teacher.
You can buy all sorts of shapes of linings (also known as kerfings) made from different woods from places like this.

Traditional Martin linings looks like: (the lining are the triangular pieces of wood near the top and bottom of the sides going all around the guitar.)

I'm going to use some traditional lining techniques but some people also use solid linings - which you heat bend to shape or laminate. And there's a "new" reverse binding technique where you put kerfed linings on backwards in an effort to add more stiffness to the sides. The structure that results has a bit of an I beam effect. Some claim this is a marvelous improvement.


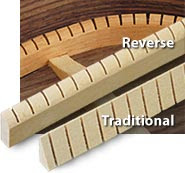
I start by slicing a pieces of Spanish cedar on a bandsaw that is about as wide as I have on hand a bit more than 3/4" thick and then using a safety planer to bring it down to 3/4". Then, I cut that into logs that are 3/4” x 5/16”. You can continue using power tools to make the linings, a table saw or band saw can be used but I'll be using hand tools from this point on.
On the left is the rough cut lining logs and on the right is the simple jig that I use to plane the log to their final shape.
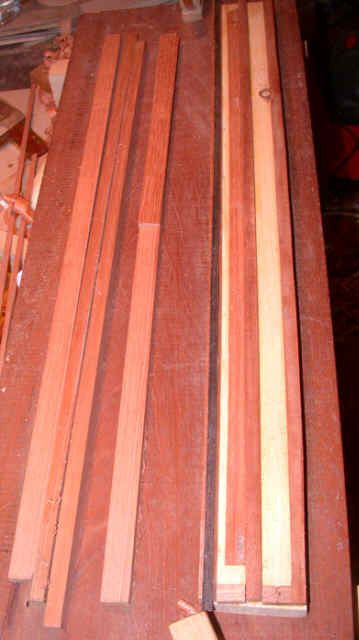
The logs were planed to their final height with the safety planer and a few passes of a hand plane before they were cut. Now they are placed into a simple jig with spacers built in for the correct width of the lining. About 1/4".
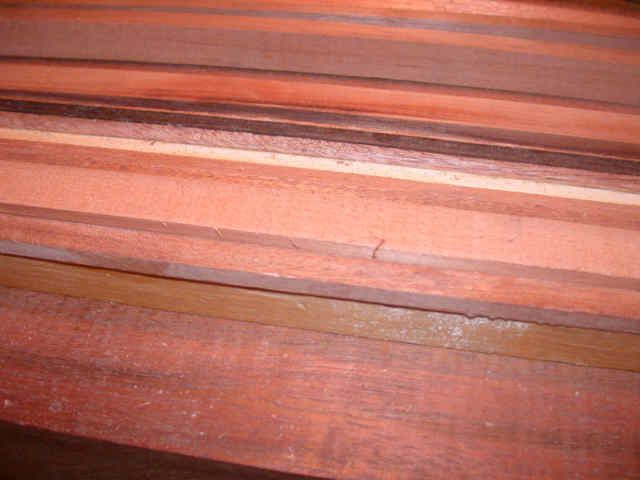
Then I plane the part of the log that's higher than the jig.
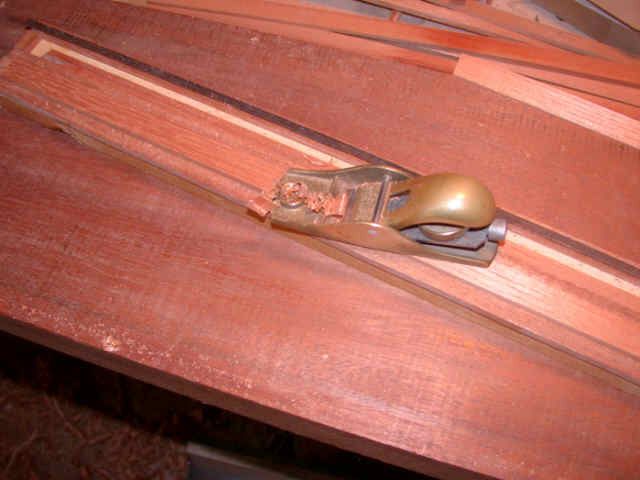
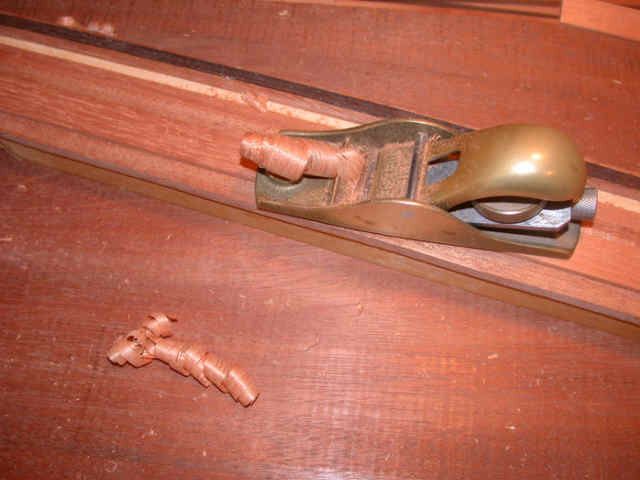
Here's another type of plane that works well for this job.
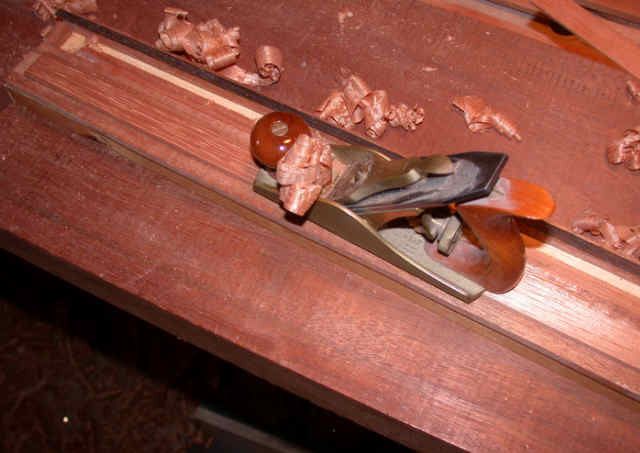
Now the height and width are set and both surfaces have been planed, not cut.
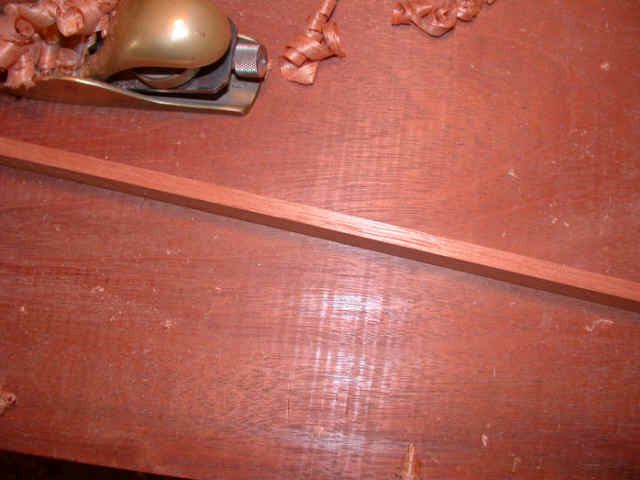
Then I transfer the log into the other side of the jig which hold it at an angle so a facet can be planed on the edge.
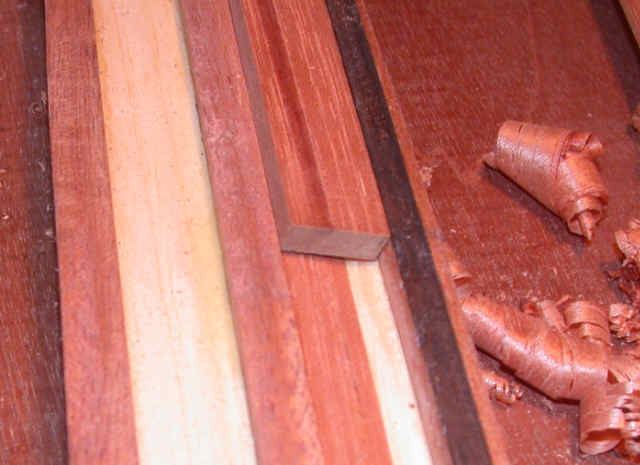
Once again, plane until the jig spacers are reached.
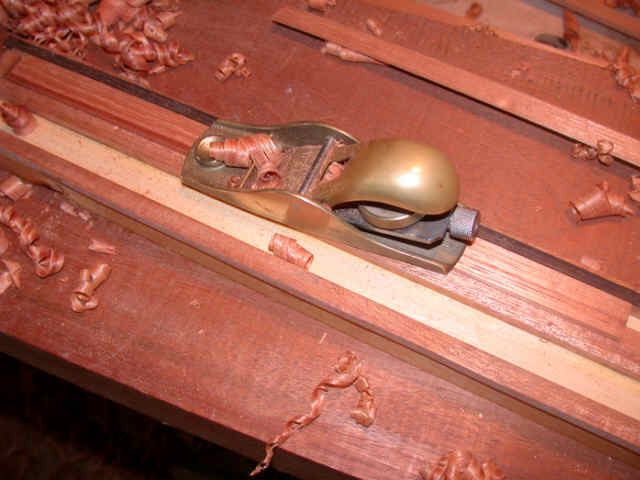
The final profile of the lining. I prefer this to a triangle but that will also work as is a bit easier to make with power tools.
Pardon my out of focus pictures.
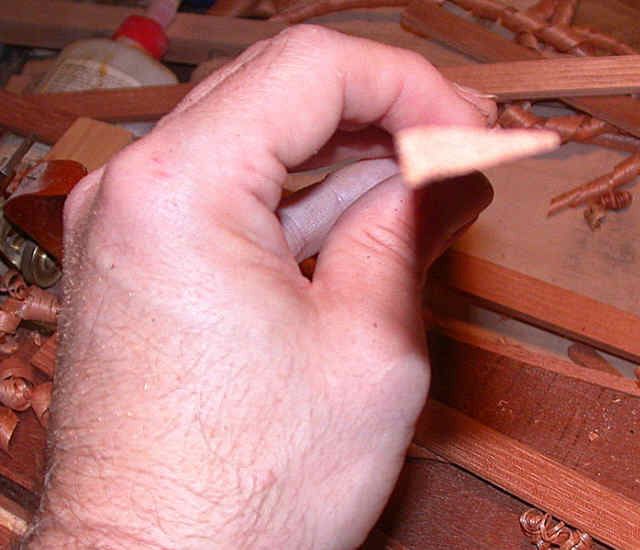
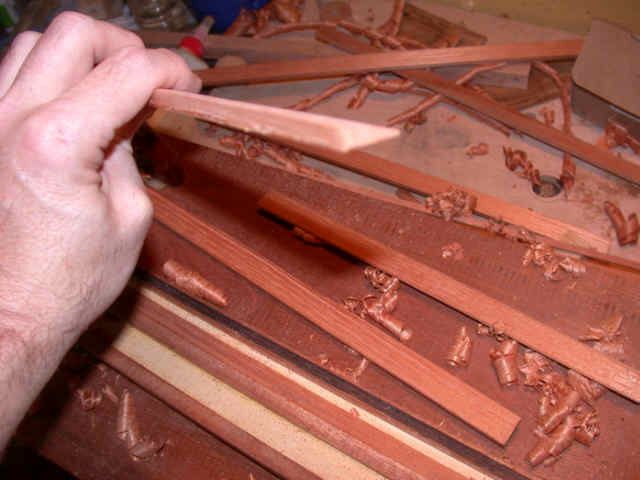
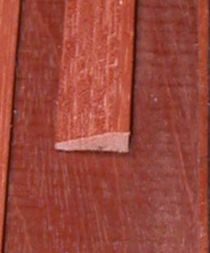
A bunch of logs are made. (on the right)
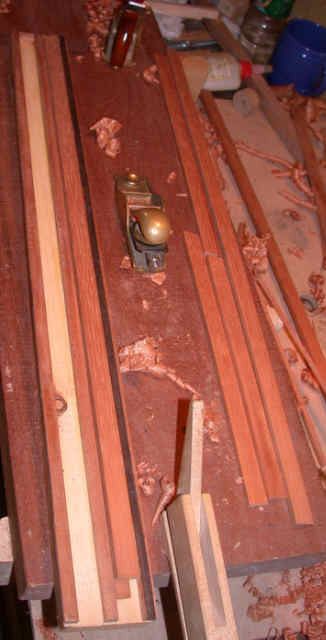